product inspection systems
Having the vision for quality control
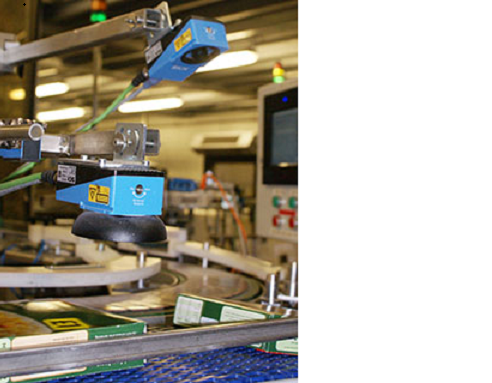
SICK said inspection is needed to ensure that packs do have on the inside what it states on the outside, especially with the number of people suffering from food allergies rising over the last few years.
Crop’s freezes large quantities of vegetables and fruit at its production site in Ooigem.
The frozen products are further processed and packaged in Ooigem as mixed stir fry vegetables, gratins, and ready meals and most of these products are taken to market as store brands.
“Our production sequences are subject to careful and comprehensive quality control, which includes the declaration of all ingredients on the relevant packaging,” said Tino Blancke, projects teamleader, responsible for production division projects at Crop’s.
“If a product should be packaged incorrectly or not have all the ingredients listed on it, the entire batch is recalled without delay.”
Two camera job
Blancke said that each packaging line is equipped with two cameras.
“One camera inspects the packaging as a whole and checks that the product sleeve has been applied correctly. The second zooms in closer and makes sure that the batch number and expiry date have been printed correctly.
“Each time the line has been changed over, an employee checks that the new packaging meets specifications.
“He then issues a command to the camera system that the packaging which follows must correspond to the recorded parameters. If there is any deviation, the camera transmits an error message and the line is stopped.
“The batch number is checked by counting pixels in the code window. If the result is too low, the product is ejected from the production line automatically.”
Line speed
To ensure the cold chain is not interrupted, quality control has to be performed within a narrow time window.
SICK said up to 100 products pass the lens every minute and the evaluation must be performed inside a fraction of a second.
Blancke said a particular reference is assigned to each format which specifies which section on the packaging the camera has to check.
“Several screens are available in the production hall, where operators can call up the images generated by the cameras. This enables us to make sure that the correct reference has been selected and that the camera is able to take a useful picture of the packaging.”
The system learns which packaging is needed for each production sequence via the teach-in function.
“If a customer changes the label layout, which happens on a regular basis because we manufacture products for store brands, the system is able to learn the parameters for the new layout automatically,” said Blancke.
“As a next step we are planning to integrate all aspects of quality control, that is, checkweighers, metal detectors, and the new vision system, into a higher-level quality assurance system so that we can also ensure seamless traceability for product control itself.”
- This case study was taken from SICK Insight Online. The firm's customer magazine.